August 10, 2009 8:50 AM CDT
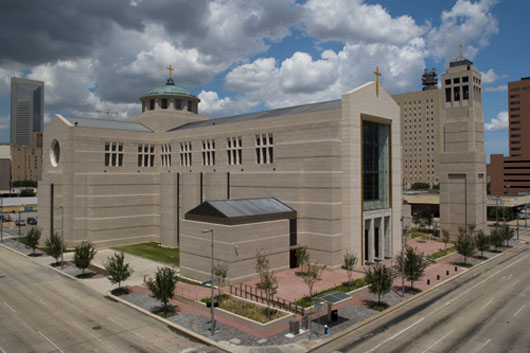
The Mason Contractors Association of America (MCAA) recently talked with Robert V. “Buddie” Barnes, Jr., Chairman of the Board and CEO of Dee Brown, Inc., about the history of his company, masonry certification, and the future of the masonry industry.
MCAA: Tell us about the history of Dee Brown, Inc.
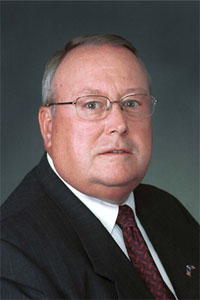
Barnes: C. DeWitt “Dee” Brown, Jr. founded our company on October 31, 1955 as a local Mason Contractor in Dallas, Texas. His mission was to provide his customers with the highest quality masonry work through dedication, reliability and integrity.
In 1969, as the company grew from a 2.5 million to 4.5 million dollars in revenue, Robert V. “Buddie” Barnes, Jr. joined the company as an estimator. It was 1977 when Dee realized that if Dee Brown, Inc. was going to maintain this growth pattern, he needed to make changes. At that point we opened division offices in both Austin and Houston, Texas. Buddie was promoted to Vice President and transferred to the Houston Division.
As DBI entered January 1985, the firm had grown to 45.0 million dollars in revenue. Buddie was transferred back to the home office as Executive Vice President and COO to manage company reorganization. By 1986 Dee Brown, Inc. was working from the east coast to the mid-west and was continuing to grow. In 1990 when the company had grown to 62.0 million in revenue per year, Dee became Chairman and CEO and Buddie became the President and COO.
Since the 1990’s Dee Brown, Inc. has been consistently recognized by Engineering News Report as one of the Top Masonry and Stone Contractors in the United States. By the mid 1990’s Robert V. “Rob” Barnes, III had joined the family business, logging time in the field, project management and estimating. This represented the beginning of the third generation of Dee Brown, Inc.
In 1999, due to his illness, Dee became Chairman Emeritus, Buddie became Chairman, President and CEO and Rob became Vice President of Estimating and Marketing. Today, as we close in on our 55th year in business, Buddie, the 2nd generation, serves as Chairman and CEO with Rob, the 3rd generation, as President and COO. He is joined by a mix of 2nd and 3rd generation employees that include his brother, John David Barnes, Vice President – Project Management and his sister, Leslie Shannon Barnes, Administrative Assistant.
We are very proud that Rob has taken our company to the next level and received the 4th National Certified Contractor Certificate issued by the Mason Contractors Association of America. We are proud that our company continues to hold strong the commitment Dee originally made to our industry and our clients by providing the highest quality masonry projects through dedication, reliability, and integrity.
MCAA: What do you think has been the key to your company’s success?
Barnes: I believe that Dee set the vision for our company by allowing us to be flexible and versatile when we needed to develop projects that did not fit the standard mold for masonry projects. Buddie, with his architectural design background, was able to expand those parameters. In doing so, he expanded our vision into the stone industry and panelization of masonry and stone products. Rob is continuing to keep our company versatile and flexible by finding and expanding into new markets with new materials. I can see that the next generation will continue to work outside the box.
I also feel that the training program we initiated in the early 1990’s, which cross-trained our field personnel, project management and estimators has allowed us to remain versatile, by keeping up with the trends of our industry. No one is just a stone mason, brick mason or a block layer, because we crossed trained all these men to allow us to respond to the needs of the marketplace. Our laborers are trained as scaffold erectors, mortar men, and mason tenders, along with working as stone setter helpers if they happened to be working in a dimensional stone setting crew. We have crossed-trained our estimators in project management and our project managers in estimating, so that they are able to support each other during peak periods whether it is in estimating or project management. We also offered all of our employees classes in Spanish to English and English to Spanish which has helped communications throughout the company.
Last, but not least, we have been able to maintain our field forces and build on them each year through the bricklaying school so that we can keep up with the aging field forces and office staff. Further, we have continued the cross-training program, and we have added first aid and safety training for everyone from labor foreman to the chairman of the board.
MCAA: What are your three biggest concerns in keeping your company successful?
Barnes: First and foremost is the ability to maintain our field work force. We have a great deal of time and money invested in our employees and we consider them part of the Dee Brown family. We have committed many hours and dollars through the years in training and will continue to do so in the future which should help us maintain a top level field operation.
Second, and truly just as important as the first, is our ability to maintain the Dee Brown vision of providing the highest quality masonry through dedication, reliability and integrity to the industry and our clients.
Dee Brown, Inc. has been recognized for its quality masonry projects by our peers at the United Masonry Contractors Association, the Texas Masonry Council and at the national level with Mason Contractors Association of America. We have also been recognized by the Building Stone Institute, Marble Institute of America, Precast Concrete Institute, American Institute of Architects, Construction Specifications Institute, the Texas Building Branch of the Associated General Contractors of America, and then locally by the Quoin and Texo Chapters of Associated General Contractors of America and the Associated Building Contractors. Dee Brown, Inc. will always strive to provide excellence in masonry for our clients and the masonry industry. I have always felt that a good reputation stays with you, but if you ever perform poorly, it will precede you and takes a long time to rid yourself of the poor performance.
MCAA: Dee Brown, Inc. was one of the first companies to become nationally certified. Why did you want to become a nationally certified mason contractor and how do you feel the certification program will benefit the masonry industry?
Barnes: We felt that it would be a win-win situation for us if we pursued the national certification program. We would increase the level of competence for all of our employees through the required training and at the same time do something that would also benefit the industry in the long run. I have always felt that you lead by example and you cannot ask other people to do something that you yourself have not done or are unwilling to do.
I know that it will not happen until sometime in the future, but when we do have enough contractors with a national certification, then the architects and owners will begin to require that the mason contractor on their project have our industry certification. We all need to remember that you must crawl before you walk and walk before you run so give the program some time. Keep constructing projects that will meet high standards in the masonry industry and we will all be winners.
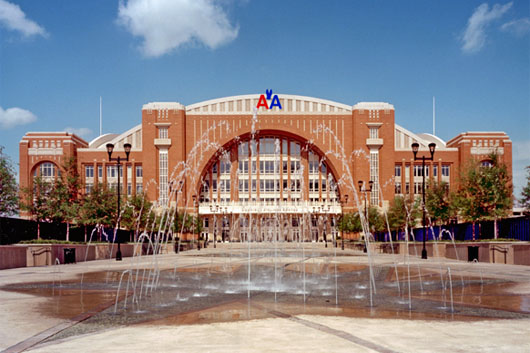
MCAA: Looking back over the years, what were some of your most difficult masonry projects, and how did you overcome the challenges those projects posed?
Barnes: In the 40 years I have been in this industry, I think I might have experienced just about every type of problem you could imagine. One fairly recent project, the American Airlines Center here in Dallas, Texas, was one I particularly enjoyed. The plans for the project called for ( 4 ) four main arches that had spans of 115’0” in width and were five stories in height without any support. It was Dee Brown’s job to figure out and recommend to the design team how we might construct the arches and what the backup support system could be. From there we met for months working out details between our engineers and the architect and engineers of record. The final backup system was job cast precast panels that were 60’0’ in length that were connected back to the structural steel and reinforced masonry walls. Then we developed 4’0’long structural brick panels that included concrete fill, rebar and embed plates to be used for the structural connections. This allowed us to start the arches at the top and go down each half of the arch. We also developed a counterweighted mechanical cradle system, which we nicknamed the “Enterprise”, that would allow the setting crew to fly the panel, which weighed over 4,000 pounds, by crane up to the point where it was to be set. Once the panel was in position the crew could then rotate the panel on the center pivot of the “Enterprise” to the exact degree needed for erection. The structural brick panels were built on the jobsite keeping things accessible. Wood forms were then placed in the trough created by the brick work allowing the rebar and embeds to be placed along with the concrete fill. The design, fabrication and erection of these panels were all done by Dee Brown Inc. on time, under cost and ahead of the construction schedule. We were able to eliminate a tremendous amount of cost and time since these arches no longer required bridging and false work. This method freed up the jobsite so that other trades had access to the project during the day while we erected the panels on second shift. We were also able to develop ( 8 ) 40”0” wide arches that were five stories in height which attached to the structural masonry using the same system as above. This project was recognized as the Masonry Construction Project of the Year in 2002.
Another truly unusual project was the Roden Crater Moon Stone Project in Arizona. The Roden Crater is a dormant volcano located in the Painted Desert in northeast Arizona. The Moon Stone Foundation, headed by artist James Turrell, owned and developed this special piece of art. We were contracted to furnish and erect the Moon Stone and all the stone paving going to and including the main chamber of the volcano. The Moon Stone was fabricated from ( 1 )one specially quarried block of Colorado White Yule Marble with dimensions of 9’0” x 9’0” x 4’0”. Cold Spring Granite fabricated this oversize piece of marble into a disc with a finished diameter of 9’0” and a thickness going from just under 4’0” to 1” at the top of the circle. They also furnished the black granite base and cap that had to be warped to fit the moon stone. The design, fabrication, and shipping of this project turned out to be the least of our problems. We found that the volcano vent passage that was to be used to move the moon stone into the main chamber of the volcano allowed for less than 2” inches of clearance between the wall of the vent and the moon stone with its rigging. After months of research and studying various types of equipment, we designed and fabricated a special cradle system. With the use of a special 80,000 lbs low profile fork lift and a lot of stress, we were able to drive the stone into the central chamber of the volcano and set it on the black granite base. Once the moon stone was in place with its cap, the granite paving could be installed and the project completed. Artist James Turrell’s vision for the project was for the moon to shine down a 900’ vent shaft into the central chamber, the moon’s reflection would be seen on the moon stone and the glow from the moon light would light the crater. This had to be one the most unusual projects in our company’s history, and the finished work of art is spectacular.
MCAA: What advice would you offer a budding mason contractor?
Barnes: First, I would say that you need to take your time growing your company, being sure that you do not over commit yourself. Many companies try to grow too fast and they wind up getting in trouble on projects by not being able to perform the work with the expertise that is required. Or, they have manpower problems both in quality and quantity which will eventually lead to financial issues, bad jobs and damaged relationships with now ex-clients.
I would also advise an up and coming company that as your projects increase in size the length of time that it will take you to receive all your money will extend out longer and create stress in your cash flow. As you grow you will find that the cash flow requirements will increase at a disproportionate rate which, in turn, will create a great deal of stress on you and your business. I also would suggest that they not be too aggressive about taking money out of the business until they have enough in reserve to operate for a year without any new work. As hard as we all try, there will be times like we are experiencing right now and that reserve may be what keeps your company viable. We are also vulnerable to that bad job now and then whether we want to admit it or not and if you did not save for that rainy day you could have severe problems.
MCAA: What do you feel is the biggest misconception about the masonry industry?
Barnes: I think that two misconceptions facing the masonry industry are 1) that there is a lack of qualified masons and mason contractors to keep up with the current work load and 2) that our work forces are getting old and that they will not keep up with the pace the industry today. Nothing could be further from the truth.
We have addressed this issue in our region with the coordinated efforts of the United Masonry Contractors Association, the Construction Education Foundation and all of the local UMCA contractor and associate members. We jointly have a mason training program that has been turning out masons in our area for more than 20 years. This program, housed at the Northlake Community College campus in Irving, Texas for the last 15 years, has enabled us to provide our students access to other classes. If they wish to pursue additional class work it can lead to an Associates Degree in construction management which they can continue through Texas A&M University – Commerce and receive a Bachelors Degree in construction science or engineering.
Through the UMCA monthly meeting, we strive to keep all of our members up to date with all information pertaining to our industry. We also encourage the UMCA members to be involved with MCAA and to attend their conferences for additional training, education and fellowship with other contractors from around the United States and Canada. We also promote the MCAA National Mason Contractor Certification program that will someday be the standard that we will all be held to.
MCAA: What would you do to change that misconception?
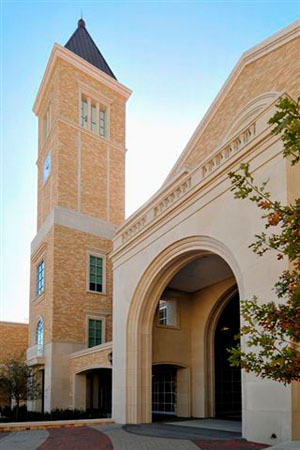
Barnes: First and foremost, we must do a better job of publicizing our industry; its accomplishments, successes, and do it through means other than just our Masonry Magazine. We have got to find ways of reaching out to the Building Owners and Developers, both private and public, and the architects and engineers that design the projects we build and let them know what is happening in our part of the industry. We need to spend less time fighting drywall and tilt wall and more time educating our consumers about the benefits of our products and how they will perform over time. We need less time on the negative and a great deal more time on the positive aspects of our industry.
Next, we need to publicize the fact that we are training masons. Let everyone know about their graduations and the great future these young men are looking at in the masonry industry. DBI provides each student, when he or she graduates, a framed certificate and a card he or she can carry showing their achievement. In each region we need to promote a general wage and benefits piece to show people who might not be headed to college that they can have a successful and financially rewarding career in the masonry industry.
And now that we have the National Mason Contractor Certification Program, we must begin to sell it to the public and make them aware of what it means and why they should be looking for the Certified Mason Contractor for all their work in the future.
Last, but not least, is to publicize the masonry and stone design and craftsmanship awards to the entire community which means national publications so that consumers are aware of the projects that have been judged exceptional and they will see what can and has been done with masonry and stone. All the local mason contractor associations in Texas have competitions which in turn submit their local winners to our state association for judging. Those winners should be submitted to the MCAA for a national judging and the winners should be recognized at the annual convention. The Building Stone Institute, the Marble Institute of America are two other associations that have similar programs and the contractors winning their awards should also be recognized. The time may have come where we should have an Industry Award program that includes all of these associations and jointly recognize the owner, architect, general contractor and the masonry and stone contractor for their achievements.
MCAA: What do you feel is the industry’s biggest challenge in the near future?
Barnes: As we have already discussed, we must do a much better job letting our clients know who we are, what we can do, and show them that we do have many capable masons and mason contractors to get their project done regardless of it’s size or complexity. The industry as a whole must do a better job promoting our contractors and our products if we are going to succeed in the future.
MCAA: What do you think the masonry industry is going to be 10 years from now?
Barnes: I think that the industry in the future will evolve into a more wall systems type construction. The contractors that can be flexible and work outside “the box” will have a very distinct advantage. The flexibility of working with various materials and knowing what new materials are available will be very important in the future.
MCAA: What do you think will be the masonry industry’s biggest competitor on 10 years?
Barnes: This is going to sound a little flippant, but I truly do not worry about what our biggest competitor might be in the future, because to me it is our own industry. If we do not raise the standards of some of the less qualified contractors; who are constructing poor quality projects, our whole industry is going to shoot itself in the foot. We must get behind the National Mason Contractor Certification Program and get it off the launch pad! We must promote and sell the Certification Program to the owners, developers, and the design community in order to prove our commitment to providing our clients with quality mason contractors who provide quality projects.
MCAA: What do you feel are the most critical issues you’ll face with future government regulations?
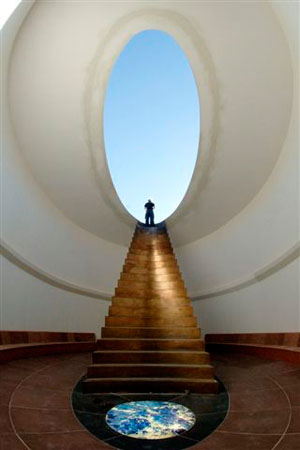
Barnes: I think you will see more difficult work rules coming from OSHA without regard as to how they truly affect the worker. We have seen several rules in the past few years that just did not work and put the worker in harms way. We have met with OSHA as a group and worked through most of these work rules as an industry with some effectiveness.
We will continue to struggle with workforce development. It is in our best interest to push forward with the training of our workers so that we can provide the qualified masons and contractors for our industry’s success.
Another issue we will continue to face is the immigration problem and illegal workers. This is a problem and I do not see any easy resolution to it. We must force our Congress in Washington to get off its hands and do their job for our country.
MCAA: Which group do you feel has the bigger impact on masonry’s future – architects, engineers, or general contractors?
Barnes: The owner has a great influence on the architect, and he will always give his direction to the architect as to the look he wants to achieve, but ultimately the architect will in my opinion be the man who controls our future.
MCAA: What do you like most about being a member of MCAA?
Barnes: The great thing about being a member of MCAA is the ability to network with other contractors who understand what you are doing as a masonry and stone contractor. In some cases in sharing issues you are dealing with, they can save you a lot of heartache because they have already been through that issue and can provide you with some answers. We also have the ability to sit down as an association to discuss many issues regarding OSHA, safety matters, and legislative issues that we individually would not get changed but collectively we may have a chance of being heard and receiving some consideration.
MCAA: Thank you for your time.
Contractor to Contractor: Dee Brown, Inc.
Past challenges, keys to success, and the future of masonry
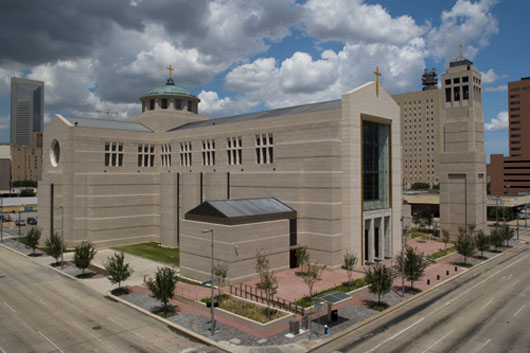
Sacred Heart Co-Cathedral. Mark Johnson Photography, Houston, Texas
The Mason Contractors Association of America (MCAA) recently talked with Robert V. “Buddie” Barnes, Jr., Chairman of the Board and CEO of Dee Brown, Inc., about the history of his company, masonry certification, and the future of the masonry industry.
MCAA: Tell us about the history of Dee Brown, Inc.
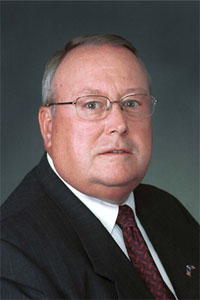
Robert V. “Buddie” Barnes, Jr., Chairman of the Board and CEO of Dee Brown, Inc.
In 1969, as the company grew from a 2.5 million to 4.5 million dollars in revenue, Robert V. “Buddie” Barnes, Jr. joined the company as an estimator. It was 1977 when Dee realized that if Dee Brown, Inc. was going to maintain this growth pattern, he needed to make changes. At that point we opened division offices in both Austin and Houston, Texas. Buddie was promoted to Vice President and transferred to the Houston Division.
As DBI entered January 1985, the firm had grown to 45.0 million dollars in revenue. Buddie was transferred back to the home office as Executive Vice President and COO to manage company reorganization. By 1986 Dee Brown, Inc. was working from the east coast to the mid-west and was continuing to grow. In 1990 when the company had grown to 62.0 million in revenue per year, Dee became Chairman and CEO and Buddie became the President and COO.
Since the 1990’s Dee Brown, Inc. has been consistently recognized by Engineering News Report as one of the Top Masonry and Stone Contractors in the United States. By the mid 1990’s Robert V. “Rob” Barnes, III had joined the family business, logging time in the field, project management and estimating. This represented the beginning of the third generation of Dee Brown, Inc.
In 1999, due to his illness, Dee became Chairman Emeritus, Buddie became Chairman, President and CEO and Rob became Vice President of Estimating and Marketing. Today, as we close in on our 55th year in business, Buddie, the 2nd generation, serves as Chairman and CEO with Rob, the 3rd generation, as President and COO. He is joined by a mix of 2nd and 3rd generation employees that include his brother, John David Barnes, Vice President – Project Management and his sister, Leslie Shannon Barnes, Administrative Assistant.
We are very proud that Rob has taken our company to the next level and received the 4th National Certified Contractor Certificate issued by the Mason Contractors Association of America. We are proud that our company continues to hold strong the commitment Dee originally made to our industry and our clients by providing the highest quality masonry projects through dedication, reliability, and integrity.
MCAA: What do you think has been the key to your company’s success?
Barnes: I believe that Dee set the vision for our company by allowing us to be flexible and versatile when we needed to develop projects that did not fit the standard mold for masonry projects. Buddie, with his architectural design background, was able to expand those parameters. In doing so, he expanded our vision into the stone industry and panelization of masonry and stone products. Rob is continuing to keep our company versatile and flexible by finding and expanding into new markets with new materials. I can see that the next generation will continue to work outside the box.
I also feel that the training program we initiated in the early 1990’s, which cross-trained our field personnel, project management and estimators has allowed us to remain versatile, by keeping up with the trends of our industry. No one is just a stone mason, brick mason or a block layer, because we crossed trained all these men to allow us to respond to the needs of the marketplace. Our laborers are trained as scaffold erectors, mortar men, and mason tenders, along with working as stone setter helpers if they happened to be working in a dimensional stone setting crew. We have crossed-trained our estimators in project management and our project managers in estimating, so that they are able to support each other during peak periods whether it is in estimating or project management. We also offered all of our employees classes in Spanish to English and English to Spanish which has helped communications throughout the company.
Last, but not least, we have been able to maintain our field forces and build on them each year through the bricklaying school so that we can keep up with the aging field forces and office staff. Further, we have continued the cross-training program, and we have added first aid and safety training for everyone from labor foreman to the chairman of the board.
MCAA: What are your three biggest concerns in keeping your company successful?
Barnes: First and foremost is the ability to maintain our field work force. We have a great deal of time and money invested in our employees and we consider them part of the Dee Brown family. We have committed many hours and dollars through the years in training and will continue to do so in the future which should help us maintain a top level field operation.
Second, and truly just as important as the first, is our ability to maintain the Dee Brown vision of providing the highest quality masonry through dedication, reliability and integrity to the industry and our clients.
Dee Brown, Inc. has been recognized for its quality masonry projects by our peers at the United Masonry Contractors Association, the Texas Masonry Council and at the national level with Mason Contractors Association of America. We have also been recognized by the Building Stone Institute, Marble Institute of America, Precast Concrete Institute, American Institute of Architects, Construction Specifications Institute, the Texas Building Branch of the Associated General Contractors of America, and then locally by the Quoin and Texo Chapters of Associated General Contractors of America and the Associated Building Contractors. Dee Brown, Inc. will always strive to provide excellence in masonry for our clients and the masonry industry. I have always felt that a good reputation stays with you, but if you ever perform poorly, it will precede you and takes a long time to rid yourself of the poor performance.
MCAA: Dee Brown, Inc. was one of the first companies to become nationally certified. Why did you want to become a nationally certified mason contractor and how do you feel the certification program will benefit the masonry industry?
Barnes: We felt that it would be a win-win situation for us if we pursued the national certification program. We would increase the level of competence for all of our employees through the required training and at the same time do something that would also benefit the industry in the long run. I have always felt that you lead by example and you cannot ask other people to do something that you yourself have not done or are unwilling to do.
I know that it will not happen until sometime in the future, but when we do have enough contractors with a national certification, then the architects and owners will begin to require that the mason contractor on their project have our industry certification. We all need to remember that you must crawl before you walk and walk before you run so give the program some time. Keep constructing projects that will meet high standards in the masonry industry and we will all be winners.
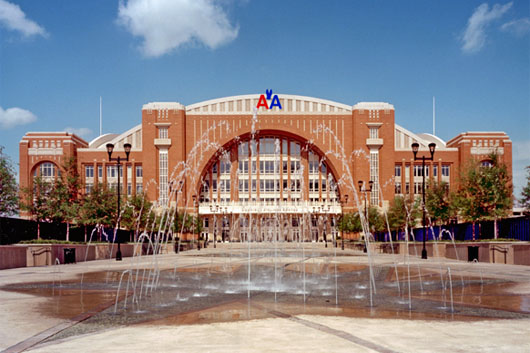
American Airlines Center: Shands Photographics, Mesquite, Texas
MCAA: Looking back over the years, what were some of your most difficult masonry projects, and how did you overcome the challenges those projects posed?
Barnes: In the 40 years I have been in this industry, I think I might have experienced just about every type of problem you could imagine. One fairly recent project, the American Airlines Center here in Dallas, Texas, was one I particularly enjoyed. The plans for the project called for ( 4 ) four main arches that had spans of 115’0” in width and were five stories in height without any support. It was Dee Brown’s job to figure out and recommend to the design team how we might construct the arches and what the backup support system could be. From there we met for months working out details between our engineers and the architect and engineers of record. The final backup system was job cast precast panels that were 60’0’ in length that were connected back to the structural steel and reinforced masonry walls. Then we developed 4’0’long structural brick panels that included concrete fill, rebar and embed plates to be used for the structural connections. This allowed us to start the arches at the top and go down each half of the arch. We also developed a counterweighted mechanical cradle system, which we nicknamed the “Enterprise”, that would allow the setting crew to fly the panel, which weighed over 4,000 pounds, by crane up to the point where it was to be set. Once the panel was in position the crew could then rotate the panel on the center pivot of the “Enterprise” to the exact degree needed for erection. The structural brick panels were built on the jobsite keeping things accessible. Wood forms were then placed in the trough created by the brick work allowing the rebar and embeds to be placed along with the concrete fill. The design, fabrication and erection of these panels were all done by Dee Brown Inc. on time, under cost and ahead of the construction schedule. We were able to eliminate a tremendous amount of cost and time since these arches no longer required bridging and false work. This method freed up the jobsite so that other trades had access to the project during the day while we erected the panels on second shift. We were also able to develop ( 8 ) 40”0” wide arches that were five stories in height which attached to the structural masonry using the same system as above. This project was recognized as the Masonry Construction Project of the Year in 2002.
Another truly unusual project was the Roden Crater Moon Stone Project in Arizona. The Roden Crater is a dormant volcano located in the Painted Desert in northeast Arizona. The Moon Stone Foundation, headed by artist James Turrell, owned and developed this special piece of art. We were contracted to furnish and erect the Moon Stone and all the stone paving going to and including the main chamber of the volcano. The Moon Stone was fabricated from ( 1 )one specially quarried block of Colorado White Yule Marble with dimensions of 9’0” x 9’0” x 4’0”. Cold Spring Granite fabricated this oversize piece of marble into a disc with a finished diameter of 9’0” and a thickness going from just under 4’0” to 1” at the top of the circle. They also furnished the black granite base and cap that had to be warped to fit the moon stone. The design, fabrication, and shipping of this project turned out to be the least of our problems. We found that the volcano vent passage that was to be used to move the moon stone into the main chamber of the volcano allowed for less than 2” inches of clearance between the wall of the vent and the moon stone with its rigging. After months of research and studying various types of equipment, we designed and fabricated a special cradle system. With the use of a special 80,000 lbs low profile fork lift and a lot of stress, we were able to drive the stone into the central chamber of the volcano and set it on the black granite base. Once the moon stone was in place with its cap, the granite paving could be installed and the project completed. Artist James Turrell’s vision for the project was for the moon to shine down a 900’ vent shaft into the central chamber, the moon’s reflection would be seen on the moon stone and the glow from the moon light would light the crater. This had to be one the most unusual projects in our company’s history, and the finished work of art is spectacular.
MCAA: What advice would you offer a budding mason contractor?
Barnes: First, I would say that you need to take your time growing your company, being sure that you do not over commit yourself. Many companies try to grow too fast and they wind up getting in trouble on projects by not being able to perform the work with the expertise that is required. Or, they have manpower problems both in quality and quantity which will eventually lead to financial issues, bad jobs and damaged relationships with now ex-clients.
I would also advise an up and coming company that as your projects increase in size the length of time that it will take you to receive all your money will extend out longer and create stress in your cash flow. As you grow you will find that the cash flow requirements will increase at a disproportionate rate which, in turn, will create a great deal of stress on you and your business. I also would suggest that they not be too aggressive about taking money out of the business until they have enough in reserve to operate for a year without any new work. As hard as we all try, there will be times like we are experiencing right now and that reserve may be what keeps your company viable. We are also vulnerable to that bad job now and then whether we want to admit it or not and if you did not save for that rainy day you could have severe problems.
MCAA: What do you feel is the biggest misconception about the masonry industry?
Barnes: I think that two misconceptions facing the masonry industry are 1) that there is a lack of qualified masons and mason contractors to keep up with the current work load and 2) that our work forces are getting old and that they will not keep up with the pace the industry today. Nothing could be further from the truth.
We have addressed this issue in our region with the coordinated efforts of the United Masonry Contractors Association, the Construction Education Foundation and all of the local UMCA contractor and associate members. We jointly have a mason training program that has been turning out masons in our area for more than 20 years. This program, housed at the Northlake Community College campus in Irving, Texas for the last 15 years, has enabled us to provide our students access to other classes. If they wish to pursue additional class work it can lead to an Associates Degree in construction management which they can continue through Texas A&M University – Commerce and receive a Bachelors Degree in construction science or engineering.
Through the UMCA monthly meeting, we strive to keep all of our members up to date with all information pertaining to our industry. We also encourage the UMCA members to be involved with MCAA and to attend their conferences for additional training, education and fellowship with other contractors from around the United States and Canada. We also promote the MCAA National Mason Contractor Certification program that will someday be the standard that we will all be held to.
MCAA: What would you do to change that misconception?
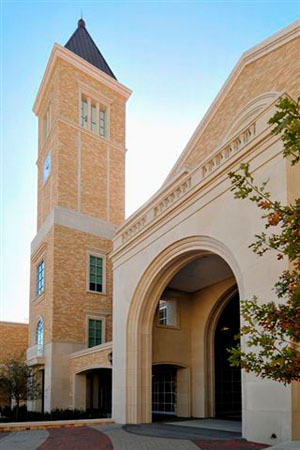
TCU Brown-Lupton Student Union: Shands Photographics, Mesquite, Texas
Next, we need to publicize the fact that we are training masons. Let everyone know about their graduations and the great future these young men are looking at in the masonry industry. DBI provides each student, when he or she graduates, a framed certificate and a card he or she can carry showing their achievement. In each region we need to promote a general wage and benefits piece to show people who might not be headed to college that they can have a successful and financially rewarding career in the masonry industry.
And now that we have the National Mason Contractor Certification Program, we must begin to sell it to the public and make them aware of what it means and why they should be looking for the Certified Mason Contractor for all their work in the future.
Last, but not least, is to publicize the masonry and stone design and craftsmanship awards to the entire community which means national publications so that consumers are aware of the projects that have been judged exceptional and they will see what can and has been done with masonry and stone. All the local mason contractor associations in Texas have competitions which in turn submit their local winners to our state association for judging. Those winners should be submitted to the MCAA for a national judging and the winners should be recognized at the annual convention. The Building Stone Institute, the Marble Institute of America are two other associations that have similar programs and the contractors winning their awards should also be recognized. The time may have come where we should have an Industry Award program that includes all of these associations and jointly recognize the owner, architect, general contractor and the masonry and stone contractor for their achievements.
MCAA: What do you feel is the industry’s biggest challenge in the near future?
Barnes: As we have already discussed, we must do a much better job letting our clients know who we are, what we can do, and show them that we do have many capable masons and mason contractors to get their project done regardless of it’s size or complexity. The industry as a whole must do a better job promoting our contractors and our products if we are going to succeed in the future.
MCAA: What do you think the masonry industry is going to be 10 years from now?
Barnes: I think that the industry in the future will evolve into a more wall systems type construction. The contractors that can be flexible and work outside “the box” will have a very distinct advantage. The flexibility of working with various materials and knowing what new materials are available will be very important in the future.
MCAA: What do you think will be the masonry industry’s biggest competitor on 10 years?
Barnes: This is going to sound a little flippant, but I truly do not worry about what our biggest competitor might be in the future, because to me it is our own industry. If we do not raise the standards of some of the less qualified contractors; who are constructing poor quality projects, our whole industry is going to shoot itself in the foot. We must get behind the National Mason Contractor Certification Program and get it off the launch pad! We must promote and sell the Certification Program to the owners, developers, and the design community in order to prove our commitment to providing our clients with quality mason contractors who provide quality projects.
MCAA: What do you feel are the most critical issues you’ll face with future government regulations?
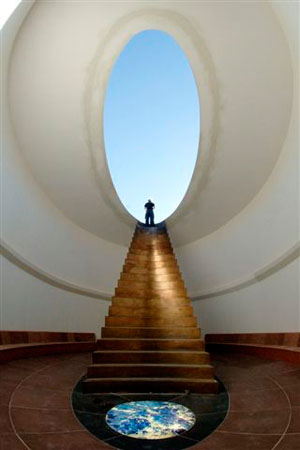
Roden Crater: Photography by Brad Goldberg
We will continue to struggle with workforce development. It is in our best interest to push forward with the training of our workers so that we can provide the qualified masons and contractors for our industry’s success.
Another issue we will continue to face is the immigration problem and illegal workers. This is a problem and I do not see any easy resolution to it. We must force our Congress in Washington to get off its hands and do their job for our country.
MCAA: Which group do you feel has the bigger impact on masonry’s future – architects, engineers, or general contractors?
Barnes: The owner has a great influence on the architect, and he will always give his direction to the architect as to the look he wants to achieve, but ultimately the architect will in my opinion be the man who controls our future.
MCAA: What do you like most about being a member of MCAA?
Barnes: The great thing about being a member of MCAA is the ability to network with other contractors who understand what you are doing as a masonry and stone contractor. In some cases in sharing issues you are dealing with, they can save you a lot of heartache because they have already been through that issue and can provide you with some answers. We also have the ability to sit down as an association to discuss many issues regarding OSHA, safety matters, and legislative issues that we individually would not get changed but collectively we may have a chance of being heard and receiving some consideration.
MCAA: Thank you for your time.
About the Author
The Mason Contractors Association of America (MCAA) is the national trade association representing mason contractors. The MCAA is committed to preserving and promoting the masonry industry by providing continuing education, advocating fair codes and standards, fostering a safe work environment, recruiting future manpower, and marketing the benefits of masonry materials.