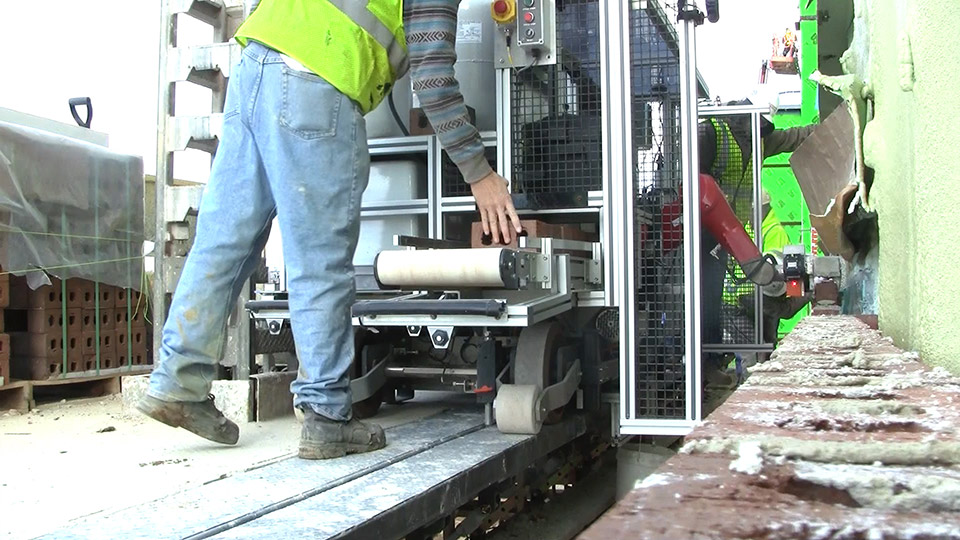
SAM100 uses a laser beam string line to accurately place a brick, while in the foreground a mason tender from Manning Construction adds bricks to the system’s conveyor.
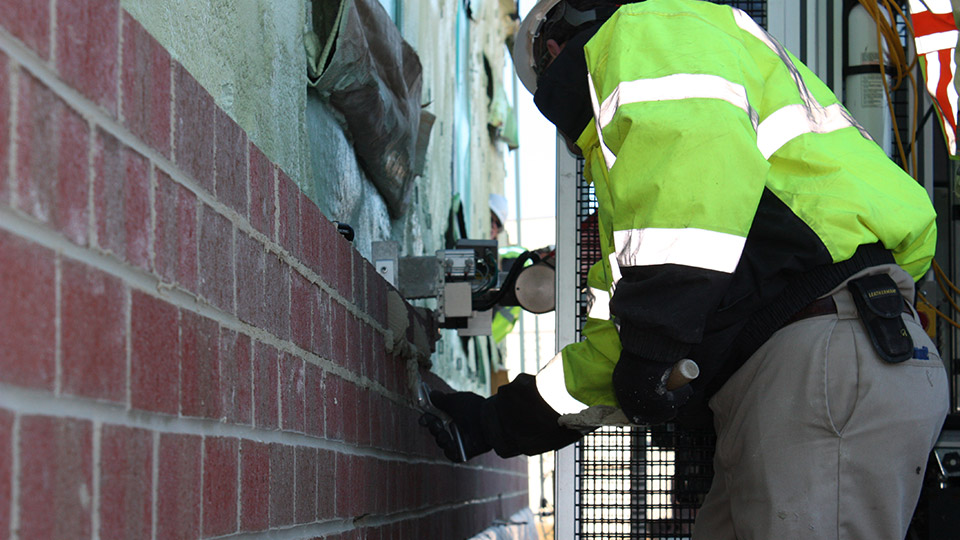
A mason from Manning Construction tools joints while working alongside SAM, the Semi-Automated Mason, on new barracks for the U.S. Army’s Fort Lee Base.