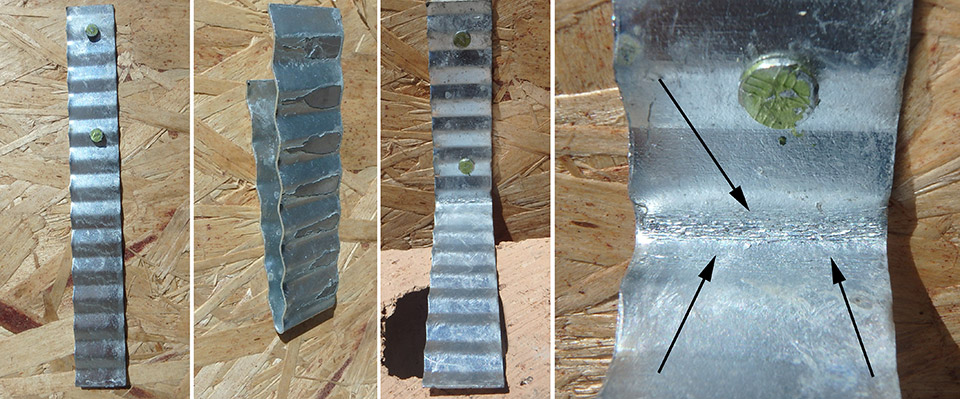
Figure 5 (from left to right): Nailed to backup; bent up 180â° to allow room for bricks; bent down 90â° when brick is installed; note cracks in the hot-dipping at the critical point of the walltie, where compression and tension loads are transferred between veneer and backup.
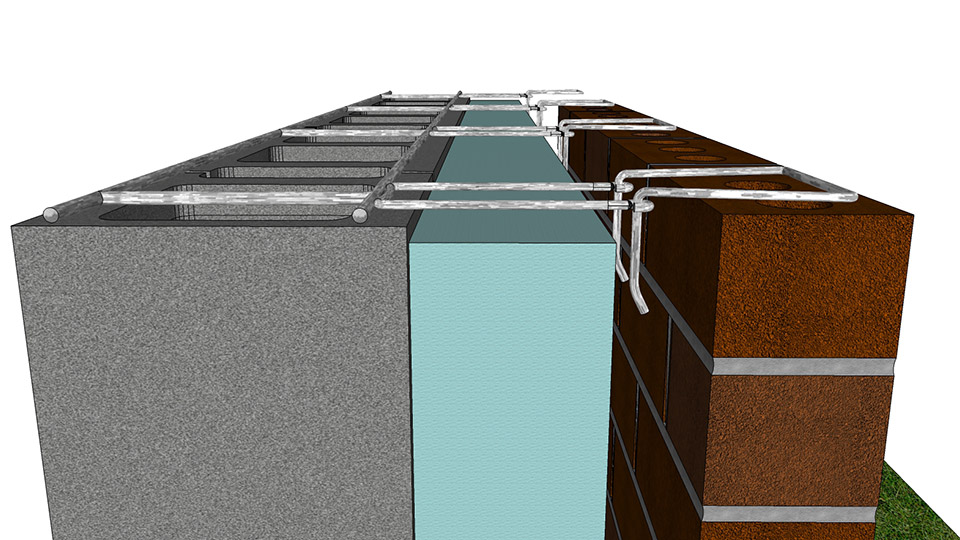
Figure 7a. Wire Reinforcement — 4-inch insulation with 2-inch airspace, 3/16-inch diameter wire spans the entire 6-inch cavity
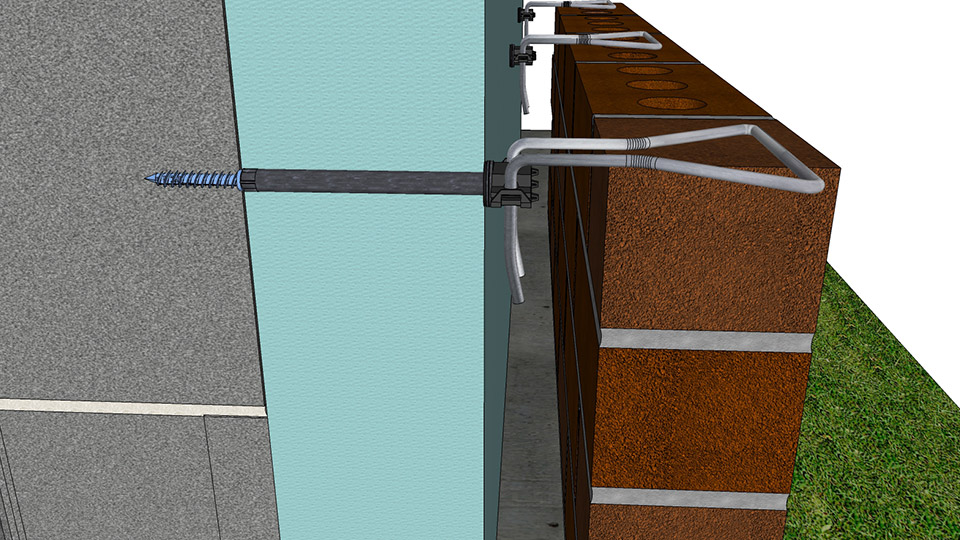
Figure 7b. Barrel Screws — 4-inch insulation with 2-inch airspace, Large diameter barrel screw goes through the 4-inch insulation, 3/16-inch diameter wire tie spans 1 3â„4 inch of the airspace, 3/16-inch diameter wire spans the entire 6-inch cavity
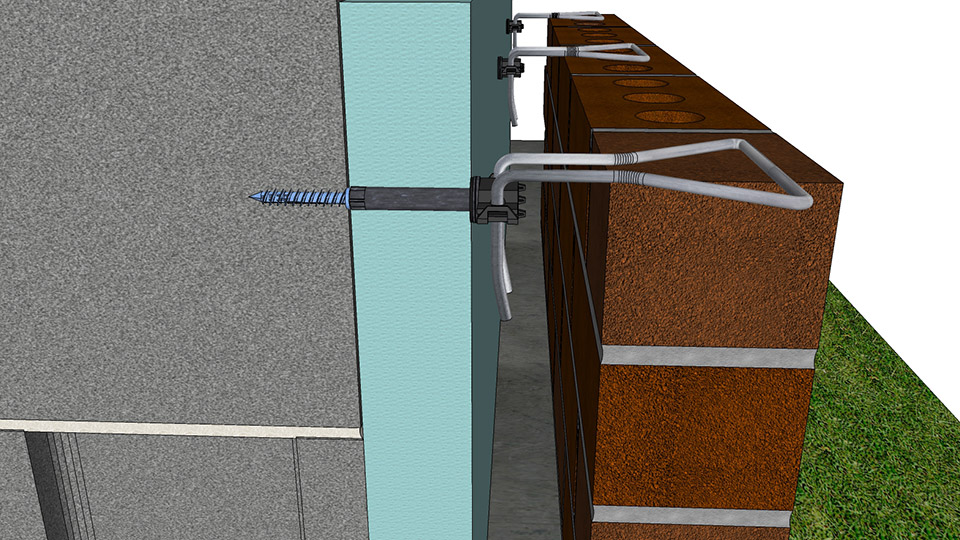
Figure 7c. Barrel Screws — 2-inch insulation with 2-inch airspace, Large diameter barrel screw goes through the 2-inch insulation, 3/16-inch diameter wire tie spans 1 3â„4 inch of the airspace