Surface mottling of mortar joints
Understanding the science of surface mottling
While masonry mortar makes up only a small percentage of the total surface area of a masonry wall, its finished appearance in a structure complements or contrasts masonry units. When the color of the mortar meets expectations, the resulting assemblage completes the designer’s vision. When the mortar color does not meet expectations, the designer’s vision is compromised.
One undesirable color variation in masonry mortar joints is surface “mottling.” Similar to mottling in concrete surfaces, mottling on mortar joints is best described as generally darkened or discolored patches or areas that are adjacent to, or within lighter colored mortar on the surface of mortar joints. Mottling generally appears during the construction phase of the project and may or may not be associated with inconsistent mortar composition. Such variation can be so random in a head or bed joint that the mortar would have to be striped or swirled on the mason’s mortar board or trowel during installation – a consistency issue easily identified by the trained of an experienced mason.
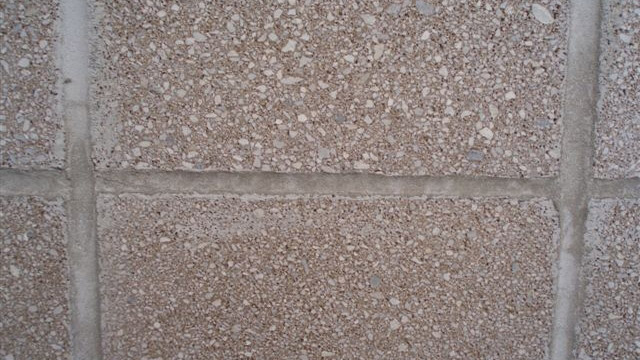
This condition of mortar joints is more common when using low initial rate of absorption and/or water repellent masonry units. In general, these units tend to repel water, which forces the water that would normally be absorbed into the masonry unit to stay in or exit through the mortar joint. This can lead to higher water contents in the mortar. To help mitigate these issues, the mortar specified for these types of masonry units should match the density and absorption properties of the masonry units as closely as possible. Mortars used for this application should generally have a low water retention and contain a water repellent admixture to properly match the masonry unit.
If the masonry unit is a polished block or glazed brick, great care should be taken in the removal of any fresh mortar smears as soon as possible. If the mortar smears are removed by rubbing the units with a rag or towel directly after tooling, mortar material adhered to the rag can be transferred to the mortar surface and water can be absorbed or added to the mortar joint contributing to surface mottling. For densified or glazed masonry units, the use of an acrylic finishing tool is generally more successful than using metal finishing tools.
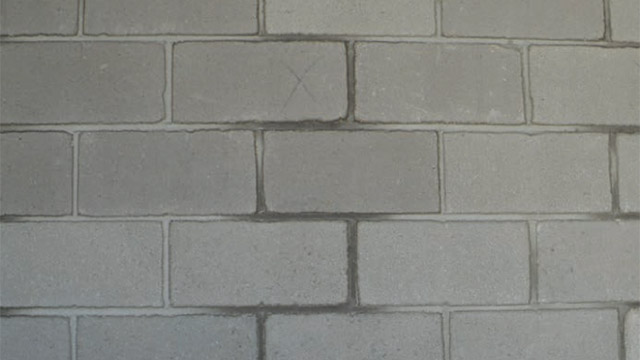
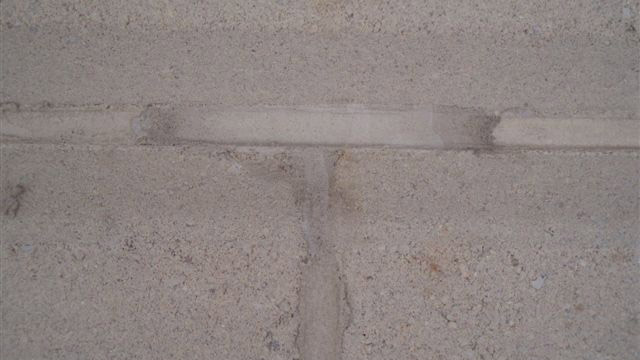
When the appearance of surface mottling occurs, an effective means of removal can be through abrasion. The manual use of a “rubbing stone” or a stone drill bit, followed with washing the joints lightly with a mild cleaning agent has proved successful in removing surface mottling.
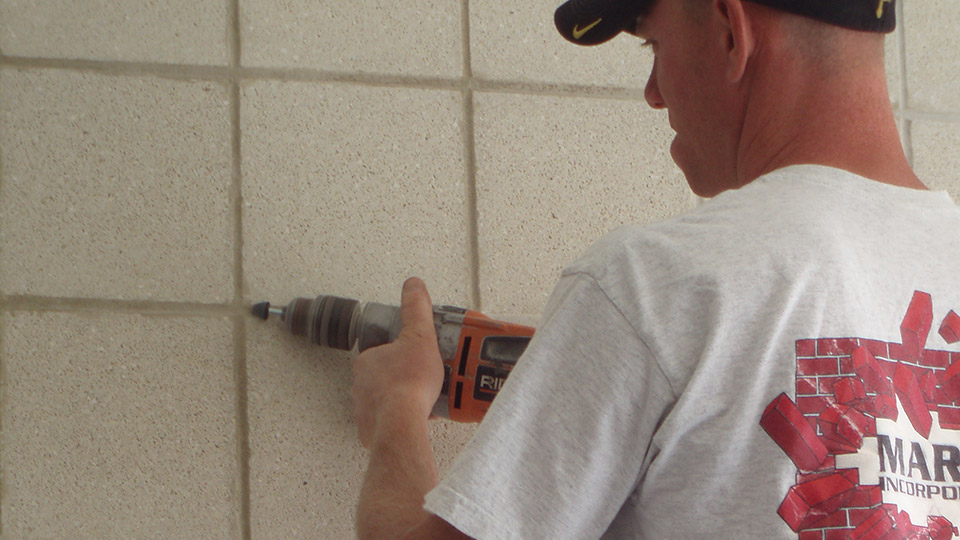
It should be noted that many manufacturers of burnished masonry units warn against the use of muriatic acid (HCl) when cleaning the wall system. If the mortar joints are washed too aggressively, the cementitious paste will become etched, exposing the aggregate. To the eye, the mortar joint will take on the color of the aggregate in the mix only, likely changing the the desired color of the joint.
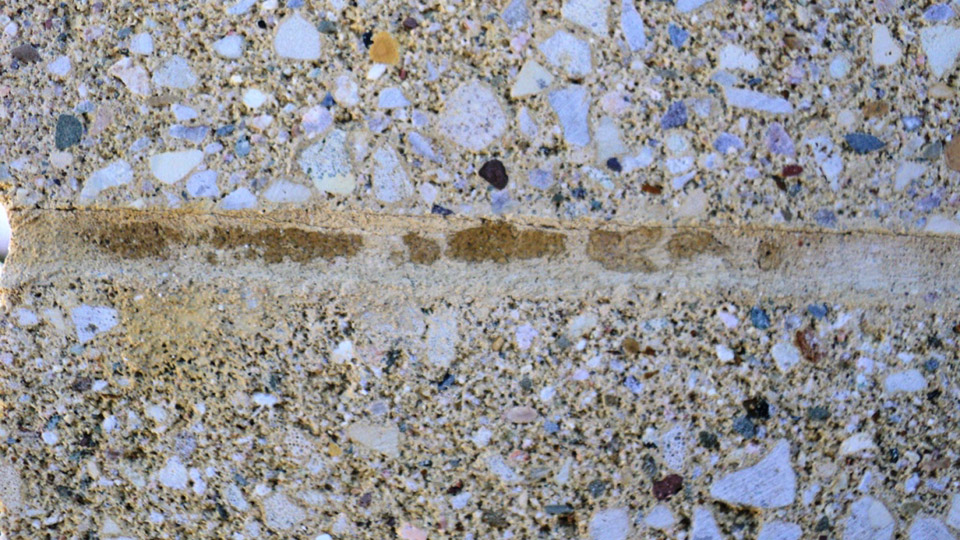
In today’s world of fast-paced construction schedules, and with the strict demands put upon mason contractors, it is critically important to understand the basic principles behind the causes of the mottling of mortar joints. Mottling can be eliminated or minimized in most instances, whereas an aesthetically pleasing finished masonry assemblage is always the result.
Work with the designer on matching the mortar type with the properties of the masonry unit. Follow proper and consistent cleaning practices, and use a reputable branded product. And remember, aggressive cleaning can burn the cement paste off the surface of the mortar joint and change the color. Make certain that consistent tooling procedures and times are put into place.
On your next project, take a step back and visualize what you can do to make sure the appearance of the mortar joints will have a true and lasting impact on your project.
About the Author
Nick Blohowiak is eastern regional sales manager for SPEC MIX Inc. He can be reached at nblohowiak@specmix.com.