March 2, 2011 7:00 AM CST
The green movement and LEED Building Rating System initiatives have swept the construction industry and taken masonry by force. Leading the way is masonry’s innate characteristic of durability. However, it is prone to create waste, and it has a lack of energy efficiency if it’s not properly insulated. Its impervious surface, when used as a ground cover, can destroy all the good this sustainable building material generates.
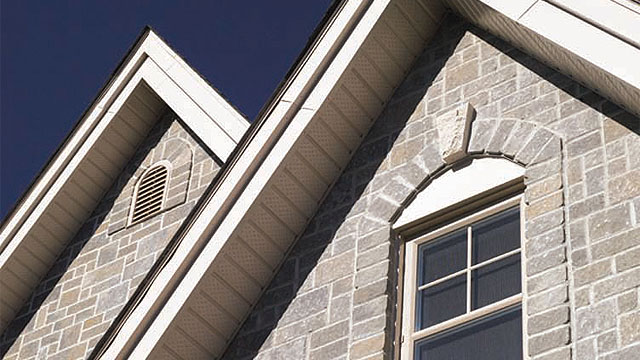
Properly installed, and more important, properly insulated, masonry veneers may well see an increase in demand from both the green and aging-in-place movements. While masonry veneers provide a low-maintenance and durable exterior solution, they also are more beautiful than other options and can produce energy savings of up to 30 percent with proper insulation. All of these benefits combined with the cost and time advantage of using a masonry veneer versus full-stone installation, makes this cladding option quite appealing to both businesses and homeowners.
A new masonry veneer system just being introduced to the U.S. market combines concrete masonry stones and clay brick with insulating polystyrene foam panels and specially designed mortar to create a veneer system with an R-13.5 insulation factor. Suretouch by Oldcastle has been growing in demand in Canada since its introduction in 2006.
SureTouch’s innovative technology pairs masonry’s durability with foam insulation panels to create an R-13.5 insulation value for energy savings and acoustical comfort. Drainage channels found on both sides of the foam panels naturally drain away any water that might infiltrate the veneer.
The foam panels are attached to the home’s exterior using stainless-steel screws and anchors. The Suretouch masonry units then are placed into pockets in the panels, taking the guesswork out of the stone placement and masonry pattern. Finally, specially designed mortar seals the system together and to the frame of the home, making a finished home exterior that is low-maintenance and durable, providing significant energy savings contributing to the home’s green status.
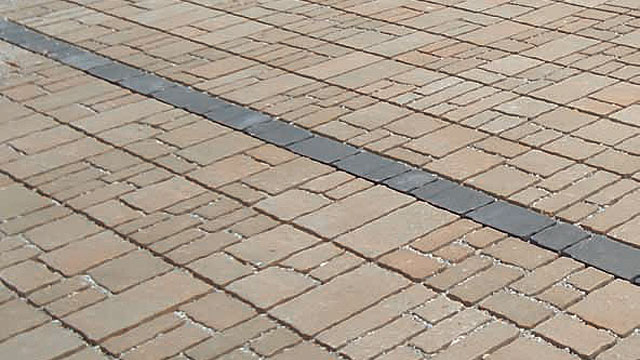
Permeable pavers are allowing governments, businesses and even homeowners to take responsibility for managing storm water runoff. As part of a bio-aquifer storm water system, permeable pavers can virtually eliminate runoff, potentially removing the need for retention ponds or underground sewer pipes.
In September, Belgard Subterra permeable pavers were used in a 9,000-square-foot parking lot at HealthNet People’s Health and Dental Center in Indianapolis. As part of a demonstration project for the City of Indianapolis’ Office of Sustainability, officials simulated a flash flood, dumping more than 4,000 gallons of water on the lot in a matter of 15 minutes. The demonstration was equivalent to the area receiving nine inches of rain. The parking lot produced no run-off.
Permeable pavers like Belgard Hardscapes Environmental collection can reduce runoff by as much as 100 percent, while providing an aesthetically pleasing and easy-to-install alternative to impervious paved surfaces. Belgard Subterra emulates the look of naturally chiseled stone, and Aqua-Roc provides a smooth surface that is comfortable for bare feet but strong enough for vehicular traffic. An additional benefit to using permeable pavers is the simple installation. The 9,000-square-foot HeathNet Center lot was installed in three weeks, and once installed, it was ready to use.
And the permeable market is not just for municipality and commercial installations. When the outdoor living trend took off in the early- to mid-2000s, it expanded the demand for outdoor masonry structures, including retaining walls, fireplaces, outdoor kitchens and decorative, yet functional, groundcovers, such as pavers. While some homeowners may not worry about the small square footage of impervious surface their outdoor living space creates, environmental stewards may be seeking a solution that is easily found through permeable pavers.
The green movement is here to stay and will only increase in demand as government regulations require more construction projects to abide by green standards and practices. With masonry’s aesthetic appeal and innate durability, it stands to gain in popularity and demand from the green movement if professionals are smart about products and practices used.
Green Building: The Changing Face of Masonry
By Oldcastle® Architectural, Inc.
Oldcastle Green Block is produced with 20% post consumer recycled glass aggregate, the equivalent of eight glass bottles.
Masonry goes back to the beginning of time, even before the astounding pyramids of Egypt. As professionals seek to emulate the natural beauty and durability of Mother Nature’s masonry wonders, such as the rock formations of Monument Valley in Utah and Arizona, we are continuously reminded of and awed by the benefits that masonry offers to commercial and residential applications. And, while beauty and durability have been the traditional appeal, the modern era has shown us a new face to masonry, and it’s green. The green movement and LEED Building Rating System initiatives have swept the construction industry and taken masonry by force. Leading the way is masonry’s innate characteristic of durability. However, it is prone to create waste, and it has a lack of energy efficiency if it’s not properly insulated. Its impervious surface, when used as a ground cover, can destroy all the good this sustainable building material generates.
Welcome Green Masonry
Innovative, new products have been designed to enhance the traditional beauty and durability of masonry, while creating sustainable solutions for the building professional.Recycled Masonry Units
The environmental impact results of products and practices used, and the actual makeup of products being used, can contribute to LEED Building Rating System points and to green building standards, in general. Today’s masonry professional has several options regarding products made from recycled construction materials. Here are a couple of products to think about:- Verastone recycled ground face masonry units from Trenwyth contain a significant amount of pre-consumer recycled content that may contribute to LEED points. The masonry units are integrally colored, pre-finished architectural concrete blocks with one or more faces ground to expose the variegated colors of the natural aggregates. They are finished with a clear, satin gloss acrylic to provide moisture resistance and enhance aesthetic appeal. The units’ flexible building application, durable quality, and recycled content make them a winning combination for building professionals.
- Oldcastle Green Block produced by Northfield-Bend in Chicago is a concrete masonry unit made with 20 percent post-consumer recycled glass aggregate, which is equivalent to eight glass bottles. The new CMU was originally designed to contribute to the green effort set forth by Mayor Daley and the city’s Olympic hopes. Oldcastle Green Block is created from recycled glass, 100 percent of which originated from the City of Chicago’s waste stream. Northfield-Bend worked closely with the Chicago recycler to create a specific aggregate gradation of glass to produce a durable, quality product to further green-building initiatives.
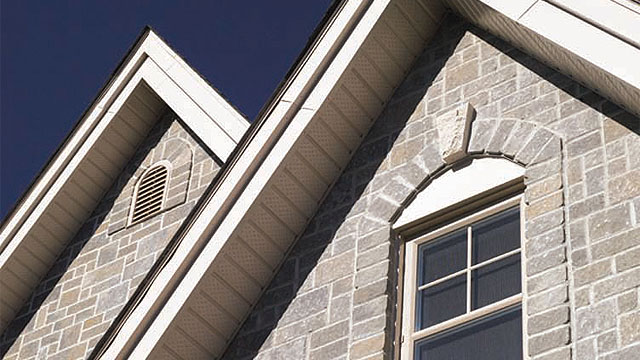
Suretouch by Oldcastle is a veneer system with an R-13.5 insulating factor for energy savings and acoustical comfort.
Masonry Veneer System
While new construction will eventually pick up, the remodeling and retrofit industry is gaining a surge from both the green movement and the aging-in-place movement. According to the AARP, older homeowners overwhelmingly prefer to age in their homes, which means that homes need to be updated to accommodate the extra years of use. The National Association of Home Builders even has a Certified Aging-in-Place Specialist (CAPS) program to accommodate the growing number of consumers who soon will require home modifications. In addition to retrofitting homes with aging friendly accessories and construction details, the aging-in-place movement also encourages low-maintenance, durable exteriors and energy-efficient updates.Properly installed, and more important, properly insulated, masonry veneers may well see an increase in demand from both the green and aging-in-place movements. While masonry veneers provide a low-maintenance and durable exterior solution, they also are more beautiful than other options and can produce energy savings of up to 30 percent with proper insulation. All of these benefits combined with the cost and time advantage of using a masonry veneer versus full-stone installation, makes this cladding option quite appealing to both businesses and homeowners.
A new masonry veneer system just being introduced to the U.S. market combines concrete masonry stones and clay brick with insulating polystyrene foam panels and specially designed mortar to create a veneer system with an R-13.5 insulation factor. Suretouch by Oldcastle has been growing in demand in Canada since its introduction in 2006.
SureTouch’s innovative technology pairs masonry’s durability with foam insulation panels to create an R-13.5 insulation value for energy savings and acoustical comfort. Drainage channels found on both sides of the foam panels naturally drain away any water that might infiltrate the veneer.
The foam panels are attached to the home’s exterior using stainless-steel screws and anchors. The Suretouch masonry units then are placed into pockets in the panels, taking the guesswork out of the stone placement and masonry pattern. Finally, specially designed mortar seals the system together and to the frame of the home, making a finished home exterior that is low-maintenance and durable, providing significant energy savings contributing to the home’s green status.
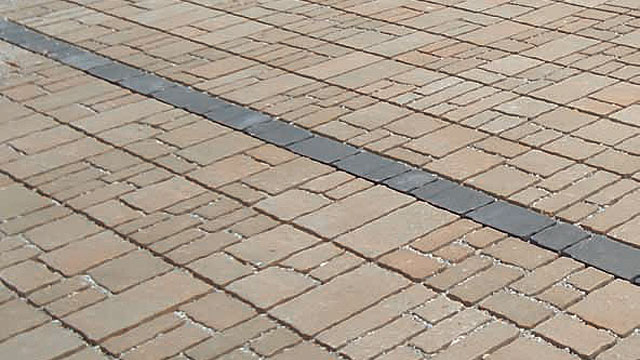
Belgard Subterra permeable pavers can reduce up to 100% of storm water runoff.
Permeable Pavers
Possibly at the top of municipality and government green initiatives lists is waste water management. As storm water runoff flows over the impervious surfaces of city streets, parking lots and paved areas, it collects debris, chemicals, sediments and other pollutants. These pollutants may pool on paved surfaces, be funneled into sewer systems or detention ponds, and eventually seep into groundwater resources or pollute larger bodies of water.Permeable pavers are allowing governments, businesses and even homeowners to take responsibility for managing storm water runoff. As part of a bio-aquifer storm water system, permeable pavers can virtually eliminate runoff, potentially removing the need for retention ponds or underground sewer pipes.
In September, Belgard Subterra permeable pavers were used in a 9,000-square-foot parking lot at HealthNet People’s Health and Dental Center in Indianapolis. As part of a demonstration project for the City of Indianapolis’ Office of Sustainability, officials simulated a flash flood, dumping more than 4,000 gallons of water on the lot in a matter of 15 minutes. The demonstration was equivalent to the area receiving nine inches of rain. The parking lot produced no run-off.
Permeable pavers like Belgard Hardscapes Environmental collection can reduce runoff by as much as 100 percent, while providing an aesthetically pleasing and easy-to-install alternative to impervious paved surfaces. Belgard Subterra emulates the look of naturally chiseled stone, and Aqua-Roc provides a smooth surface that is comfortable for bare feet but strong enough for vehicular traffic. An additional benefit to using permeable pavers is the simple installation. The 9,000-square-foot HeathNet Center lot was installed in three weeks, and once installed, it was ready to use.
And the permeable market is not just for municipality and commercial installations. When the outdoor living trend took off in the early- to mid-2000s, it expanded the demand for outdoor masonry structures, including retaining walls, fireplaces, outdoor kitchens and decorative, yet functional, groundcovers, such as pavers. While some homeowners may not worry about the small square footage of impervious surface their outdoor living space creates, environmental stewards may be seeking a solution that is easily found through permeable pavers.
The green movement is here to stay and will only increase in demand as government regulations require more construction projects to abide by green standards and practices. With masonry’s aesthetic appeal and innate durability, it stands to gain in popularity and demand from the green movement if professionals are smart about products and practices used.
Originally published in Masonry magazine.
About the Author
Oldcastle® Architectural, Inc. is North America’s leading producer of concrete for the following markets: commercial masonry, professional landscaping and consumer DIY. For more information, visit www.oldcastleapg.com, or call 770-804-3363.