Climb the ladder
To improve wall reinforcing design
A grass roots effort is under way to modernize the way CMU horizontal wire reinforcing is manufactured, packaged, shipped and installed in North America. These changes, if implemented, will greatly enhance bricklayer productivity by optimizing lapping and narrowing the profile (height) where the pintles are welded to the wire.
For decades masons have been rightfully complaining about using truss wire in reinforced CMU and the difficulty of using lap welded adjustable wire reinforcing in CMU back-ups. As most CMU today is vertically reinforced the urgency to upgrade has reached the critical stage. Truss wire creates a problem when diagonal cross wires obstruct the core, interfering with the placement of vertical reinforcing, making it nearly impossible to meet minimum grouting standards. Ladder wire with 16" o.c. (on center) cross rods placed on the webs of the CMU keeps the core clear of obstructions that could restrict the placement of vertical reinforcing or the flow of grout.
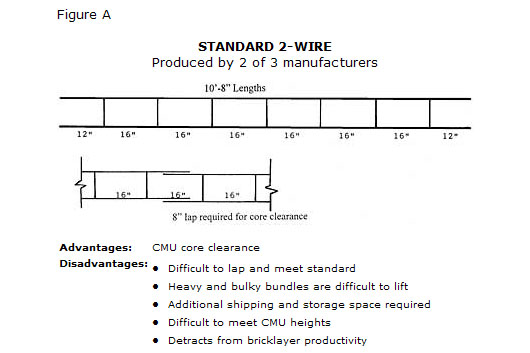
Presently, two out of three manufacturers' produce standard 10'- 8" length wire with cross rods spaced 16" o.c. starting 8" off each end (Figure A). The third produces 16" o.c. wire by special order only. They continue to produce the majority of their wire 10' - 0" under the old standard with cross rods spaced 15" o.c. This is unfortunate because 15" o.c. makes it impossible for the mason to line up the cross rods on the webs of the CMU, again, making it difficult to ensure vertical core clearance for rebar and grout installation.
Masonry Reinforcing Corporation of America (MRCA) should be applauded for the giant leap they took in the winter of 98 to make the initial conversion with Dur-O-Wal following last winter. But many improvements remain before we start back slapping. The 16" o.c. cross rods are optimum for grouting but the 8" distance of the first cross rod off each end makes it difficult to lap the wire to meet the 6" minimum standard and maintain core clearance. The cross rods at the laps are within 8" of each other and this often results in an overlap instead of a side lap. Wire manufactured 10' - 0" long with cross rods 12" from each end and 16" o.c. would eliminate the risk of overlap by optimizing cross rod spacing on the webs of the CMU (Figure B). The best part about making these changes is that they don't need any approval. In fact, these changes will bring these materials closer to the design intent and installation criteria of architects', engineers' and mason contractors'.
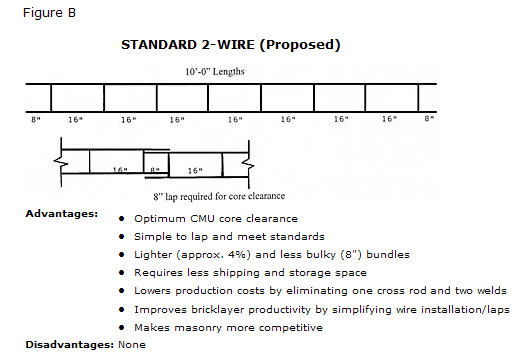
MRCA and Dur-O-Wal produce adjustable hook & eye wire with the side rods starting 8" from each end with 3/16" dia. pintle eyes lap-welded on the top of the wire at the cross rods (Figure C). Hohmann & Barnard produces hook & eye with cross rods spaced approximately 15" o.c. with 3/16" dia. pintles welded 16" o.c. on the outer longitudinal wire. Pintles lap welded on top of the wire compounds the difficulty of installation, making it impossible for the bricklayer to meet the 6" lap standard or to maintain modular wall heights. Flush-welding pintles to the outer face of the proposed 16" o.c. 2-wire will narrow the wire profile (Figure D), overcoming the disadvantages of the present standard and significantly improving bricklayer productivity.
At the time of this writing the three major wire manufacturers have been slow to recognize the changing landscape of CMU construction. The days of truss wire, 15" o.c. ladder, and lap-welded adjustable wire are fading. Although they haven't yet dedicated production capacity to producing these new ladder systems they all claim to have stepped up research and development and plan to meet demand when it reaches a practical volume. There is no doubt that a bold move by any one of these producers would soon become the industry standard for adjustable and 2-wire reinforcing as the advantages of these configurations would reach every facet of our industry.
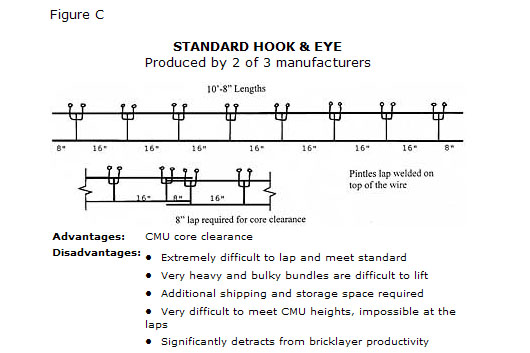
Mason contractors benefit from these two changes with wire that easily meets industry lapping standards, simplifies rebar installation and improves gout flow. Narrowing the profile of adjustable wire will improve bricklayer productivity by up to 15%, with less time installing the wire itself and improving their ability to meet modular heights. Contractors can reduce worker's compensation risk with shorter wire bundles (with one less cross rod and one less and shorter pintle eyes) that are lighter and easier to handle.
In addition to the workers compensation issue, masonry distributors will gain with yard storage and shipping capacity. Both changes will result in bundles that are at least 8" shorter while flush-welded eyes narrow 250 lf bundles by two inches. Yard capacity requirements can be reduced and shipping capacity on trucks can be increased by 25-30%. This change will improve truckload stability by eliminating the spring in bundles.
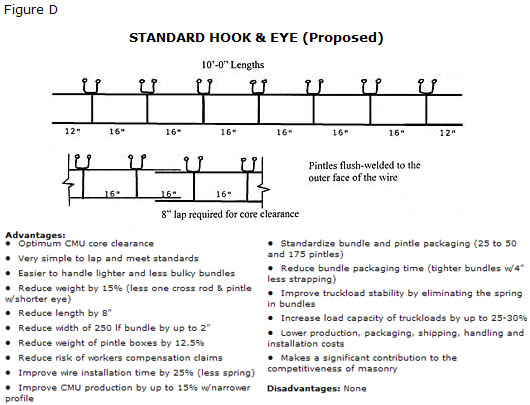
Manufacturers gain for all of the same reasons as mason contractors and distributors, with the additional benefit of lowering their production, packaging, and shipping costs. In addition, this system standardizes pintle packaging to match the quantities of all of their adjustable wire configurations.
So, you ask, what's taking so long? In short, the manufacturers have failed to recognize the fact that most wire reinforcing is not lapped according to the standards, in fact, most wire is butted end-to-end or if it is lapped it is likely causing the restrictions described above. The initial cost to upgrade the production equipment could be recaptured in a relatively short period with the savings from lower production, packaging and shipping costs described above.
The time has come for bricklayers, mason contractors, block producers, distributors, architects and engineers to encourage wire producers to make these changes. We will all benefit from a product that significantly improves the effectiveness and competitiveness of masonry.
About the Authors
Kyle Lochonic is a Project Manager for Davenport Masonry, Inc.
Jeff Snyder is the owner of MASONPRO, Inc. in Northville, Mich.